1
/
of
1
SUPERWIN303
SUPERWIN303: Link Daftar Situs Slot Pragmatic Gacor Terpercaya 2024 Hari Ini
SUPERWIN303: Link Daftar Situs Slot Pragmatic Gacor Terpercaya 2024 Hari Ini

Regular price
Rp 25.000,00
Regular price
Rp 50.000,00
Sale price
Rp 25.000,00
Unit price
/
per
Couldn't load pickup availability
superwin303 merupakan situs slot dana 10k bonus garansi kekalahan 100 saldo cashback terpercaya 2024 penyedia game slot dana gacor gampang jackpot dengan bocoran pola gacor hari ini.
Bonus garansi kekalahan 100 adalah bonus deposit new member superwin303 hanya dengan deposit 10k di sini kamu bisa main game slot gacor 2024 dan bisa mendapatkan kemenangan jutaan rupiah hanya dengan modal receh di situs slot gacor no.1 di indonesia
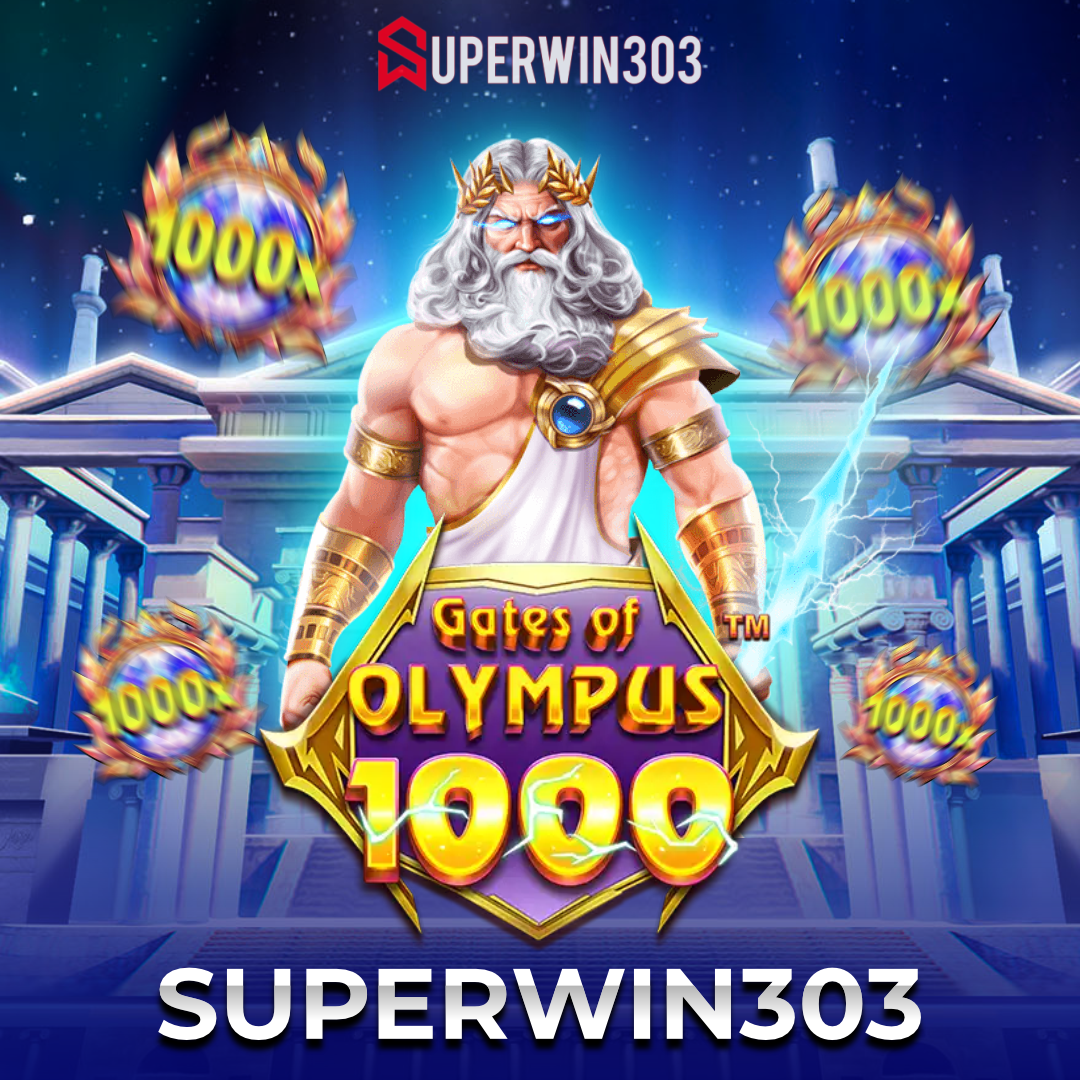